Introduction: Modern Plywood Wine Rack
I made a modern, wall-hanging wine rack with stemware storage from a single sheet of inexpensive plywood. This project had some challenges along the way, so be sure to watch the video and follow along with me through this build.
Step 1: BACKGROUND
The guys over at The Modern Maker Podcast (@ModernBuilds @Benjaminuyeda & @FourEyesFurniture on Instagram) wanted to challenge people to create something around a single sheet of plywood.
For this challenge, they didn't want to get very specific about the things you could not use, but rather just say that you should mostly use no more than one sheet of plywood. They didn't even specify which type of plywood to use, so there was a lot of opportunity for creativity.
I wanted to take part in the challenge, so I started thinking about what I would like to make. I landed upon a modern wine rack that had integrated stemware storage. My vision is that this would be a wall hanging wine rack, with kind of a boxy shape. Then, it would have holes cut in the face to accept the wine bottles. In each of the holes, I would paint a color to give it a little pop.
I debated cutting strips of plywood and gluing them back together to make a panel where all of the plys would show, but I decided against that method. Instead, I featured just a little of the exposed plywood edge on each of the side, using a half lap rabbet to join the sides together.
Then, my next thought was to build this using a single sheet of walnut plywood. I have never ordered it, so I started researching where to even get it. In my area, Home Depot can get it, but it takes a month to arrive! A month! I just didn't have time to wait on it.
I landed on one sheet of radiata pine plywood. It is sold as 3/4", but it is actually 23/32", so just a little shy of 3/4". It has a pretty nice look to it, and the laminations on the edge look really nice. One sheet of this stuff is about $23.
Step 2: TOOLS & MATERIALS
Table Saw - https://amzn.to/2G1zdwj
Random orbit sander - http://amzn.to/2GPjaUo
Bandsaw (same model as mine, but mine is anniversary edition)- http://amzn.to/2BI2xJV
Drill & driver - http://amzn.to/2BI2xJV
Miter saw - http://amzn.to/2BI2xJV
Walnut dowels - http://amzn.to/2BI2xJV
Glue brush - http://amzn.to/2BI2xJV
Step 3: STEPS - Start With a Sketch
I did a few rough sketches for what I wanted this piece to look like. I am not good at drawing at all, but I wanted to get some ideas and parameters down so I could use it as a starting point.
There were some things I either knew I had to use or wanted to use:
Plywood
Dowels
Paint in a small amount
Step 4: PLYWOOD
It is important to start with plywood that is very flat and straight. I did NOT do this, so don't do like I did.
Once I noticed that the plywood was very bowed, they had already cut it in half at The Home Depot. I've started doing this while at the store, so I don't have to try to borrow a truck to get a whole sheet home. I don't have a truck right now. Anyway, once they cut the sheet, I bought it.
When I got all of the pieces home, I put a bunch of weight on top of them on the floor in hopes to flatten them out some. I'm not sure it made much of a difference at all, but it sure made me feel better.
Step 5: TEMPLATE
Next, I put together a few sheets of paper and made a full-scale template. I just drew out a grid, and started laying out everything where I thought it should go. I used one of the pieces of stemware I had and a wine bottle I had to arrive at some of the dimensions. Then, it was just a matter of laying it all out in an eye-pleasing way.
I used a compass to help me envision what it would look like, and so that it would be easier to mark for drilling out the holes later.
Step 6: THE CARCASS
I cut the main carcass out on the table saw. If you remember, these had already been cut down a decent amount while at the store, so they were very manageable panels.
Once I got the long side of it cut, I was able to use my crosscut sled on my table saw to cut the other side.
Step 7: MARK FOR HOLES
Next, I laid the template I made onto the correctly-sized work piece, and used a center punch to mark all of my holes. This little divot helps the drill bit to find exactly where it needs to go.
Step 8: DRILL HOLES
I used a 2" forstner bit to drill out as many of the holes at the drill press as I could. Some of them were deep enough into the board, I could not get to them with the drill press. I had to use a handheld drill for those.
Step 9: CUT a RABBET
The next part was intimidating for me - using a dado stack in the table saw. I had never done this until this project, and while it turned out just fine, I was intimidated by it at first.
I just took my time to understand all about how it works, and they did a lot of testing on scraps. When I finally had it all dialed in, I referenced one side of the work piece against the table saw fence, allowing a rabbet to be cut on one end of the work piece.
This rabbet went through exactly one half of the thickness of the plywood, so that when I did the same to the sides of the wine rack, they would mate together nicely.
Step 10: SUPPORTS PIECES
I cut some small support pieces from some of the leftover bits of plywood. These would be used to create the ledge on the backside of each hole that would actually hold the necks of the wine bottles. While I was designing and testing this out, I figured out that the wine bottles would not sit at an upward angle unless there was some space between the face of the piece and where the necks of the bottles held. These created that space.
Step 11: PAINT
I prepped the holes by giving them a light sanding. Then, I put some painter's tape over the front of the holes. I then flipped the piece over and sprayed some paint from the back. This allowed the color to get inside the hole and on the sides of each hole, but when I pulled the tape away on the front, I had nice, clean paint lines.
Step 12: WINE BOTTLE SUPPORTS
The supports across the back that are spaced one piece of plywood away from the front piece (as noted in the previous step) need to cover part of the holes. I just used some glue and brad nails to add these to the back.
Then, gluing on the sides with the rabbets was a really tricky part because the plywood was so warped. I eventually got clamps on it and got it pretty well straight.
Step 13: DRILL FOR DOWELS
I wanted to use some walnut dowels to pin the sides. That way, it would give some contrast to the pine plywood I used, and help with strength as well. I didn't want to use any screws in this piece. I didn't have a real reason for not wanting to use screws, but I just didn't.
The lines I marked would make it where when I would drill the hole, it would be right in the center of the plywood edge. Taking a little extra time on this part is really useful, since it will look nicer if your dowels are spaced perfectly even and you don't have a blowout with your drill for drilling a hole too close to one of the sides.
QUICK TIP:
If you have a certain depth you need to drill to, and you're using a handheld drill, mark that spot on your drill bit using a little flag made from painter's tape. Then, as you're drilling, and there are shavings all over the face of your work piece, when you see it get cleaned off by the flag as it spins around, you know you've reached your desired depth. I will often use this if I have a lot of holes that I need to drill. This project was a perfect use case of it, I had over 20 holes to drill!
Step 14: CUT & PLACE DOWELS
I set up a stop block on my miter saw so I could cut 6 dowels at about 8" long. These would be to hold the stemware. For the smaller, 1.5" pieces I needed as joinery, I cut them out on the bandsaw (not pictured).
Then, I applied some glue to the dowels and the holes, and hammered them in with a small, brass mallet. I like using this mallet for hammering in dowels, because it is not too bulky, but still has enough heft to get the job done.
Step 15: FIX MISTAKE
As I was drilling out some of the large holes by hand, the forstner bit jumped out of one of the holes and really marred the surface. I didn't have any extra plywood that was large enough, since this was already the second piece this size. The first one, I messed up with my first design. (I didn't end up really wasting any of it though, because I got some of the strips for the back support and sides out of that piece.)
I was trying to figure out a way to fix this when I talked to my friend, Doug. He has the YouTube channel DN Handcrafted, and has a really great mind for figuring out solutions to problems. He has some great videos on his channel, so go watch some of those.
Anyway, Doug and I talked for a few minutes and he had the idea to just laser cut a piece of walnut plywood that was slightly larger than the hole, and make that a design element. I thought about doing it as an inlay at first, but ended up just layering it on top. I think it just added some dimension to the piece.
So, I designed a quick circle to the specs I needed in Inkscape, and used my Glowforge to cut it out of some walnut plywood. It worked great! I glued that piece on and used some large pieces of scrap steel as gravity clamps.
Step 16: SANDING
I sanded the piece with some 120 grit, then 220 grit sand paper using the random orbit sander. Then, I broke all of the edges by hand.
Step 17: FINISHING
I used some brushing lacquer for finish. I wiped on a thin coat for the first one. Then, I sanded in between coats with 320 grit sandpaper. I brushed on two more coats, sanding in between. I'm able to achieve a very smooth finish with this method.
Step 18: CONCLUSION
Thank you for following along with this project! If you haven't already, watch the video. Also, leave me a comment and let me know what you think. I'd love to hear if you would have done it differently in any way. See you on the next project!
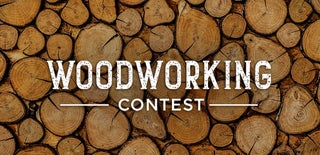
Participated in the
Woodworking Contest